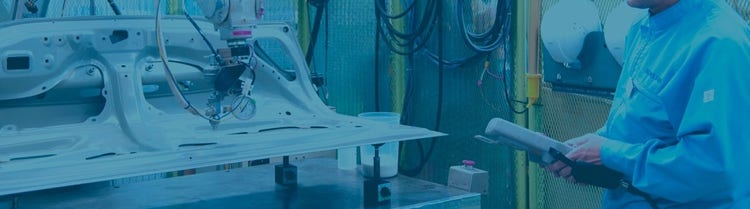
AUTOMOTIVE ADHESIVES & SEALANTS
Specialty
- Formed‐in‐Place Foamed Gasket
- Underfill Material
- Liquid‐applied UV‐Curable Masking Material
Specialty Engineered Products
At Sunstar, we provide the advanced engineering automotive manufacturers trust for the performance and integrity of their vehicles. That advanced engineering has produced a line of specialty products developed to address distinct manufacturing needs.
Formed‐in‐Place Foamed Gasket (FIPFG)
Sunstar offers multiple one‐component gasket formulations to meet specific needs. Our one‐ component liquid foam gasket technology provides a fast and cost‐effective gasket solution. Our proprietary mechanical foaming machine (FOAMPLY) produces a mechanically foamed gasket for a high‐quality, precise gasket application with low scrap and low labor requirements.
Distinct Benefits
- Efficient, low‐temperature curing. Sunstar’s proprietary technology promotes fast curing at 80°C, substantially reducing gasket processing time over conventional methods.
- Outstanding sealing performance. Sunstar’s proprietary mechanical foaming system (FOAMPLY) facilitates application of a uniform closed‐cell gasket. The system provides tight, repeatable dimensions. The resulting gasket delivers excellent water, air, and dust sealing performance.
- A wide range of solutions. In addition to our standard products, we offer a wide range of specialty form‐in‐place foamed gasket products including heat‐resistant, slow‐ burning, adhesive, and plasticizer‐free products.
Production process
Applicable substrates
✓ Full adhesion / – Not recommended
Curing method
Application parts
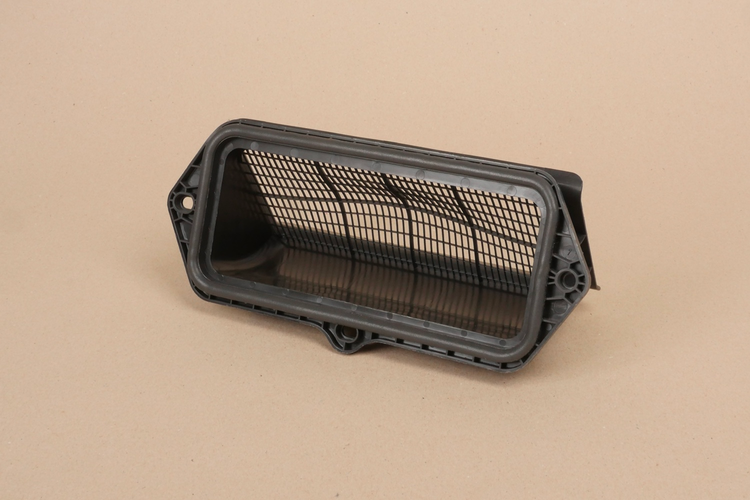
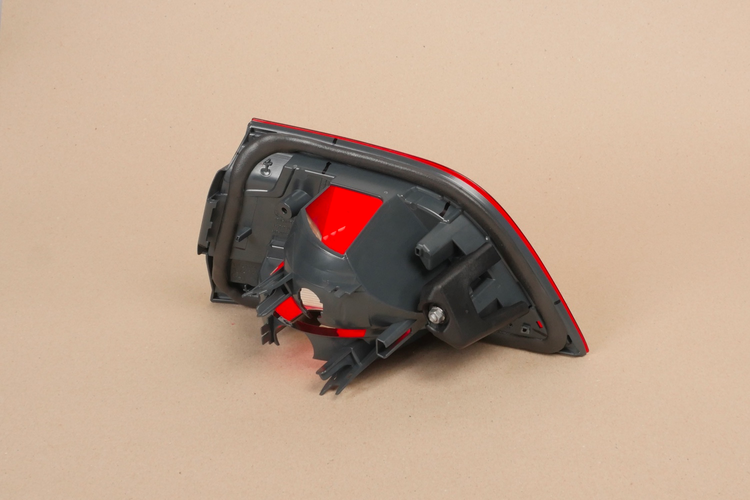
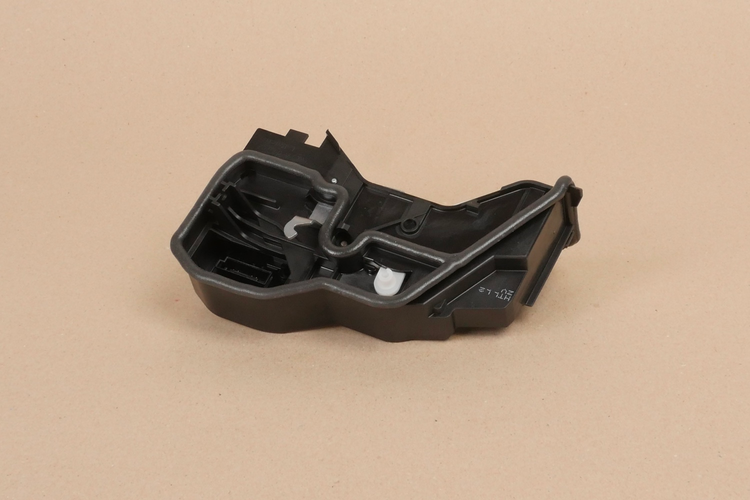
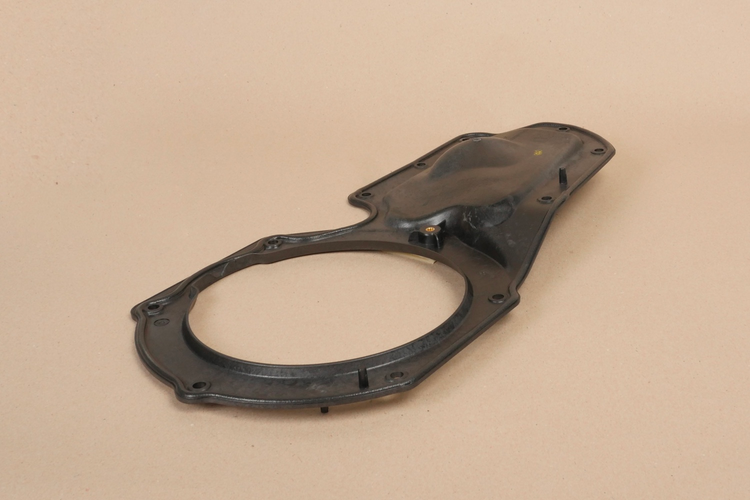
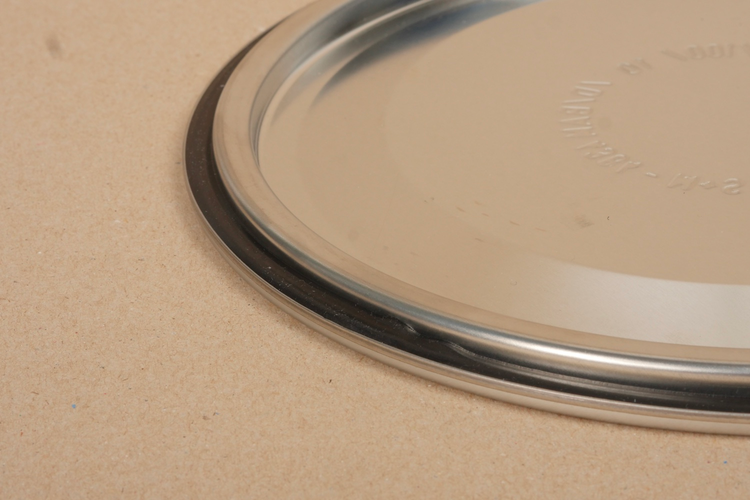
- Air filter unit
- Door speaker
- ECU/Relay-BOX
- Maintenance lid cover
- Rear gate cover
- Weatherstrip
- Cockpit module
- Dush board unit
- Fuse box cover
- Outer pillar cover
- Side part of dash panel
Underfill Material
Our exclusive Underfill Material solutions significantly improve the durability and reliability of automotive electronic components by protecting their soldered connections from common thermal stresses and vibrations.
Distinct Benefits
- Improved heat cycling property. Epoxy resin with dispersed silicone cross‐linked particles is used to absorb strains between the circuit board and the device. It suppresses solder cracks due to heat cycling.
- High electrical insulation property. Thanks to its high heat resistance and low moisture absorption design, our Underfill Material provides excellent electrical insulation property even in high temperature and high humidity conditions.
- Superior permeability. Our Underfill Material is engineered to have low‐viscosity properties when heated, providing exceptional permeability, which is ideal for narrow gap parts.
Production process
Applicable substrates
✓ Full adhesion / – Not recommended
Curing method
Application parts
- Onboard Camera/Sensor
- ECU (Electronic Control Unit)
- Digital cockpit
Liquid‐applied, UV‐curable Masking Material
Sunstar offers an ultra‐efficient automated masking method that replaces labor‐intensive hand taping. Our liquid‐applied, UV‐cured masking material produces excellent masking precision while reducing application and removal process time. The UV curing process, which can be completed as applied, is nearly instantaneous.
Distinct Benefits
- Cures in seconds. Since it’s a UV‐cured material, the time loss associated with traditional curing is eliminated. A UV light can be positioned to chase the robotic applicator, curing the material as applied, or a simple stationary clamshell UV station can quickly irradiate the material. Either way, curing takes less than three seconds.
Thin application. Excellent strength. Application thickness is less than 300 microns and adheres to a wide variety of substrates. The material withstands the high heat of the OEM paint line environment—up to 190‐degrees Celsius—and presents tremendous cohesive strength. - Clean edge lines. The applicator provides a thin ribbon with sharp, clean edge lines for a consistent, precise paint line.
- No residue. This advanced masking material is easily removed and leaves no residue behind.
Production process
Applicable substrates
✓ Full adhesion / – Not recommended
Curing method
Application parts
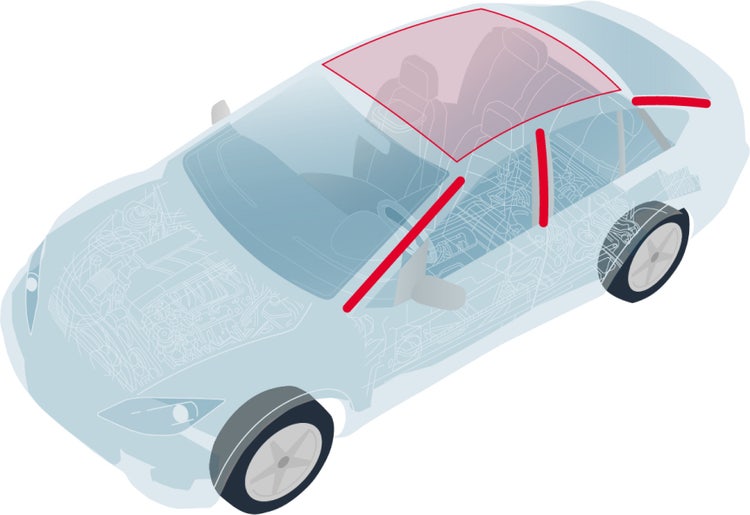
We’re ready to help
Contact us to find out how our advanced engineering solutions can help your business
Trusted by the world’s leading companies to solve unique engineering challenges
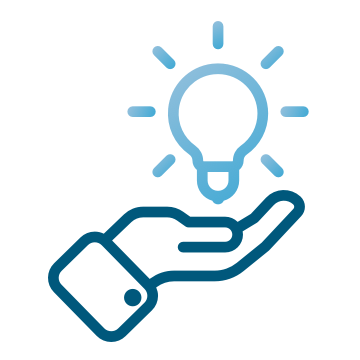
Your innovation partner
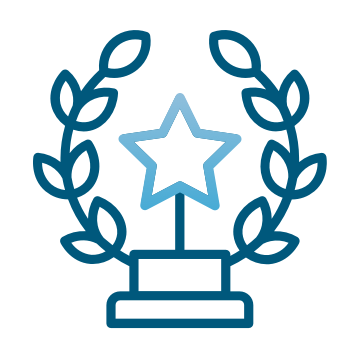
chosen by the best
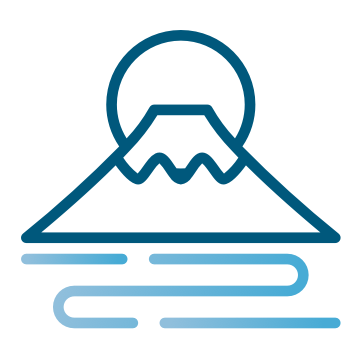